Blackbike
Retro Guru
Re: Re:
Your bottom bracket has a lot more in common with a lathe spindle than a conventional bottom bracket see the attached photo, instead of a lathe chuck imagine a crank arm and chain ring. Timken bearings are shown in the photo, imagine annular contact ball bearings instead. I believe whoever designed your bottom bracket spent time in a machine shop as it's constructed like a lathe spindle.
Let's assemble the bottom bracket, first the outer bearing races are pressed into the bottom bracket shell until contact is made with a step or shoulder internal to the shell.
Next the right hand inner bearing race is pressed on the right hand side of the spindle against the shoulder and then the ball bearings and retainer is placed on top of the inner race and inserted as an assembly into the outer race through the right hand side of the bottom bracket.
The left hand ball bearings and retainer is set in the outer bearing race and the inner bearing race is a slip fit over the shaft until contact is made with the bearings and races.
The two nuts controll bearing preload, the snap ring, dust shield, and felts are not a structural part of any of this and only keep the grease in and the weather out.
The bearings in your bottom bracket are similar to the type used in Maxi-car hubs and old school high speed rotating machinery, they are very stout and handle axial and thrust loads. Your bearings have numbers stamped on the edges of the races and should be available at any good bearing house.
I hope this helps, the reason I said "Wow!!!" in my first post was I recognised the construction from my machine shop days. :shock:
: Mike
bduc61":2z8xlhnp said:Well guessed, the grease seals are felt !
and the right side is most probably very similar to the left but without bolts - see pic below - have to undo it
By the way why did you say it could be taken out on the right side ? I would have thought the other way around ?
As to me the bolts compress the left handside spindle part so that it can not move outside to the left - the spindle being blocked against a move towards the right by the right washer blocked by the open ring - the right bearings being blocked to the right by the same washer and to the left by a shoulder on the spindle ! ouch dunno if it is understandable and making sense at the same time :mrgreen:
Your bottom bracket has a lot more in common with a lathe spindle than a conventional bottom bracket see the attached photo, instead of a lathe chuck imagine a crank arm and chain ring. Timken bearings are shown in the photo, imagine annular contact ball bearings instead. I believe whoever designed your bottom bracket spent time in a machine shop as it's constructed like a lathe spindle.
Let's assemble the bottom bracket, first the outer bearing races are pressed into the bottom bracket shell until contact is made with a step or shoulder internal to the shell.
Next the right hand inner bearing race is pressed on the right hand side of the spindle against the shoulder and then the ball bearings and retainer is placed on top of the inner race and inserted as an assembly into the outer race through the right hand side of the bottom bracket.
The left hand ball bearings and retainer is set in the outer bearing race and the inner bearing race is a slip fit over the shaft until contact is made with the bearings and races.
The two nuts controll bearing preload, the snap ring, dust shield, and felts are not a structural part of any of this and only keep the grease in and the weather out.
The bearings in your bottom bracket are similar to the type used in Maxi-car hubs and old school high speed rotating machinery, they are very stout and handle axial and thrust loads. Your bearings have numbers stamped on the edges of the races and should be available at any good bearing house.
I hope this helps, the reason I said "Wow!!!" in my first post was I recognised the construction from my machine shop days. :shock:
: Mike
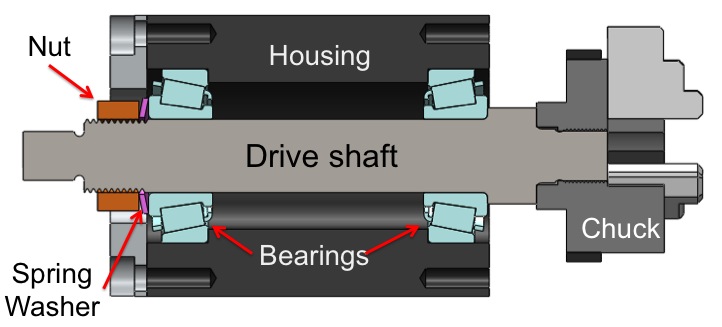