I have been asked a few times now about cutting or extending fork threads. As I keep most of my long PM's (to save me writing them again
) this one is pretty much copied / pasted with a few photos added in 
This is what the 'professional' did at my LBS, this wasn't the trainee, this was the 'old' owner of a long standing / traditional shop :
If its not obvious to see, the thread is pretty mashed / almost non existent in places making the cup and locknut a very loose fit that wouldn't tighten properly or squarely :-(
That was the reason I acquired a new set of forks, borrowed a tool and cut the threads myself ...
This is the tool I borrowed :
And here are the instructions I wrote :
Well it's actually dead easy ! No black art, no great skills etc - just a bit of care, attention and patience
• First up, remove the part of the tool that guides the die down the steerer. It will be a tool steel collar. Make sure this goes down the steerer without snagging or jamming on stamping, paint, paint runs or plastic lining etc (clean up where nessasary). The tighter the fit the better, but you don't want it to jam or snag.
• Remove the die from the tool.
• Clean everything of swarf.
• Refit the die and the collar. Ensure they are fully seated and square to the tool i.e. no crap under them.
• The die may be the split type (not a complete circle / donut). If it is, make sure it is secure but don't compress it. If you do it will cut a slightly smaller / looser thread.
• Clamp the forks in a wooden work bench (wrapped in a cloth) so as not to mark them. Make sure the steerer is vertical - it will be much easier to see if the thread is cutting straight / as it should.
• Cover the lower half of the thread in whatever cutting compound or oil you have.
• Carefully slide the guide onto the steerer and ensure the thread of the die engages properly.
• Wind it down to the bottom of the existing thread.
• Time to start cutting - it will require quite a lot of force ...
• Turn the tool about 1/8 th of a turn max.
• Back the tool off about a 1/16 th of a turn.
• Repeat above two steps.
• During the process do the following things religiously :
1) Stand back from the job and check everything is running square / true.
2) Apply cutting compound / oil when nessasary - never let it cut dry.
3) Clear the swarf as often as possible.
• If you don't clear the swarf often it 'could' get dragged back into the tool marking the finish of the thread a little. It 'could' make the tool harder to turn.
• It will take a while. Go slowly / carefully.
Good luck and let us know how you go on
This was the finished thread, you can see the colour change of the new threads :
And then cut down to suit :
It works perfectly :
Hope that helps !
WD


This is what the 'professional' did at my LBS, this wasn't the trainee, this was the 'old' owner of a long standing / traditional shop :
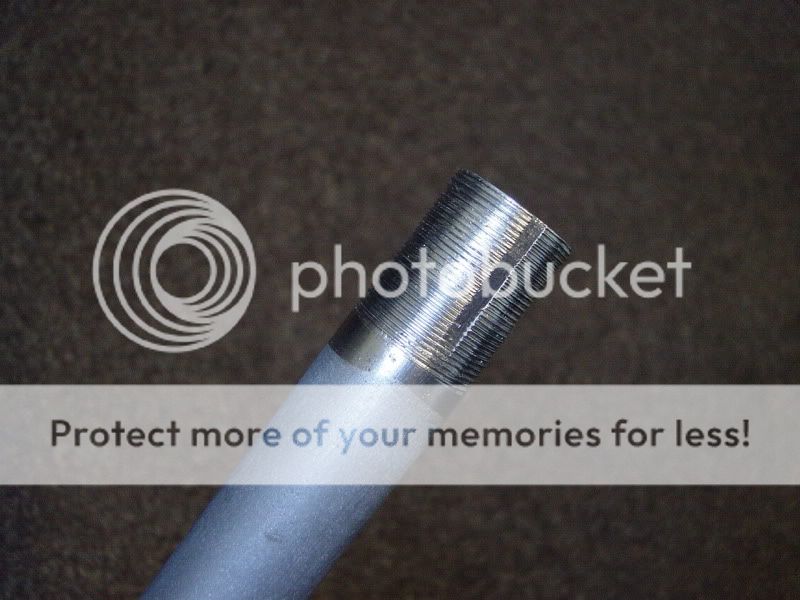
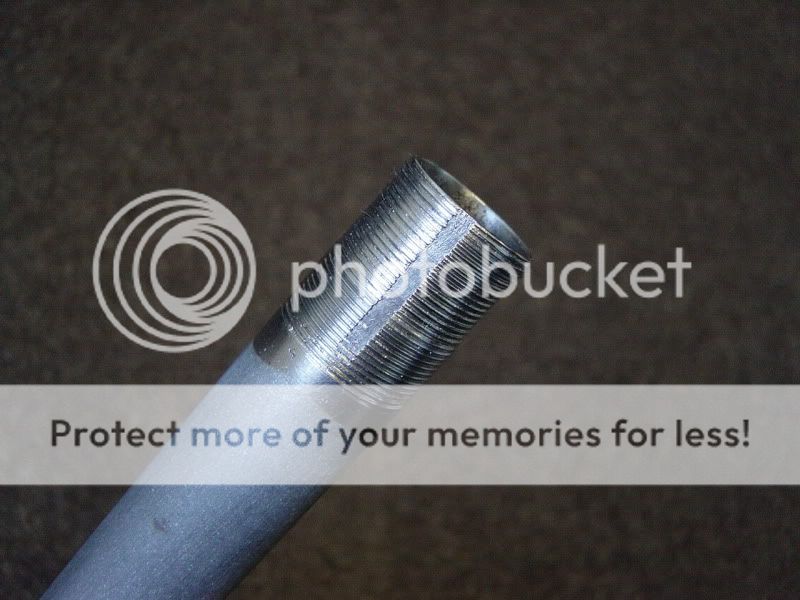
If its not obvious to see, the thread is pretty mashed / almost non existent in places making the cup and locknut a very loose fit that wouldn't tighten properly or squarely :-(
That was the reason I acquired a new set of forks, borrowed a tool and cut the threads myself ...
This is the tool I borrowed :
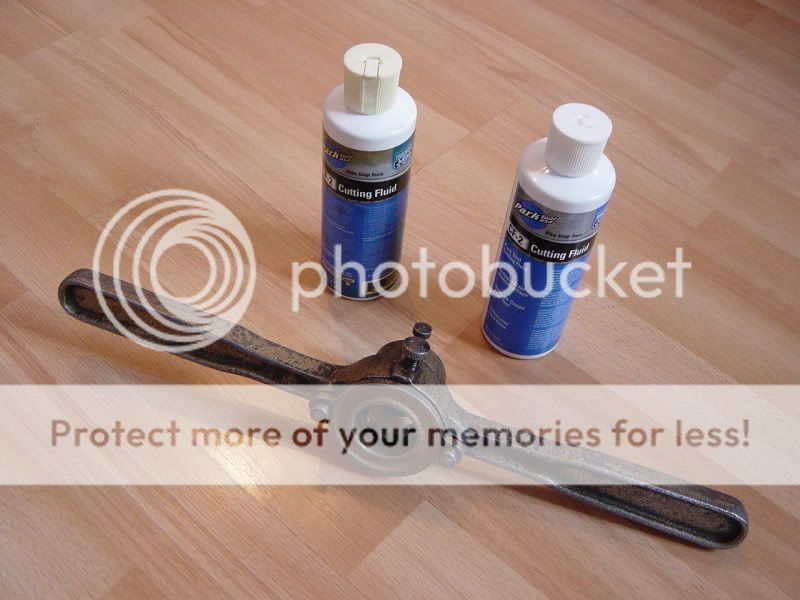
And here are the instructions I wrote :
Well it's actually dead easy ! No black art, no great skills etc - just a bit of care, attention and patience

• First up, remove the part of the tool that guides the die down the steerer. It will be a tool steel collar. Make sure this goes down the steerer without snagging or jamming on stamping, paint, paint runs or plastic lining etc (clean up where nessasary). The tighter the fit the better, but you don't want it to jam or snag.
• Remove the die from the tool.
• Clean everything of swarf.
• Refit the die and the collar. Ensure they are fully seated and square to the tool i.e. no crap under them.
• The die may be the split type (not a complete circle / donut). If it is, make sure it is secure but don't compress it. If you do it will cut a slightly smaller / looser thread.
• Clamp the forks in a wooden work bench (wrapped in a cloth) so as not to mark them. Make sure the steerer is vertical - it will be much easier to see if the thread is cutting straight / as it should.
• Cover the lower half of the thread in whatever cutting compound or oil you have.
• Carefully slide the guide onto the steerer and ensure the thread of the die engages properly.
• Wind it down to the bottom of the existing thread.
• Time to start cutting - it will require quite a lot of force ...
• Turn the tool about 1/8 th of a turn max.
• Back the tool off about a 1/16 th of a turn.
• Repeat above two steps.
• During the process do the following things religiously :
1) Stand back from the job and check everything is running square / true.
2) Apply cutting compound / oil when nessasary - never let it cut dry.
3) Clear the swarf as often as possible.
• If you don't clear the swarf often it 'could' get dragged back into the tool marking the finish of the thread a little. It 'could' make the tool harder to turn.
• It will take a while. Go slowly / carefully.
Good luck and let us know how you go on

This was the finished thread, you can see the colour change of the new threads :
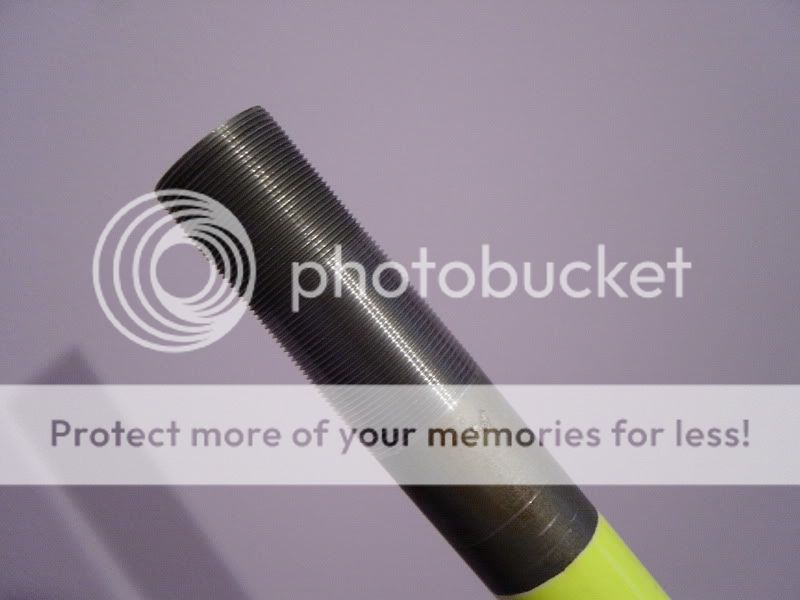
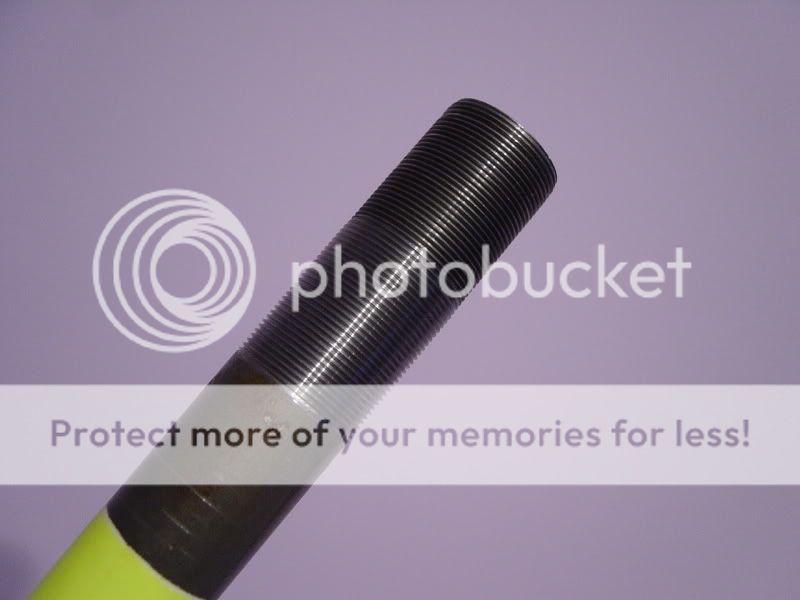
And then cut down to suit :
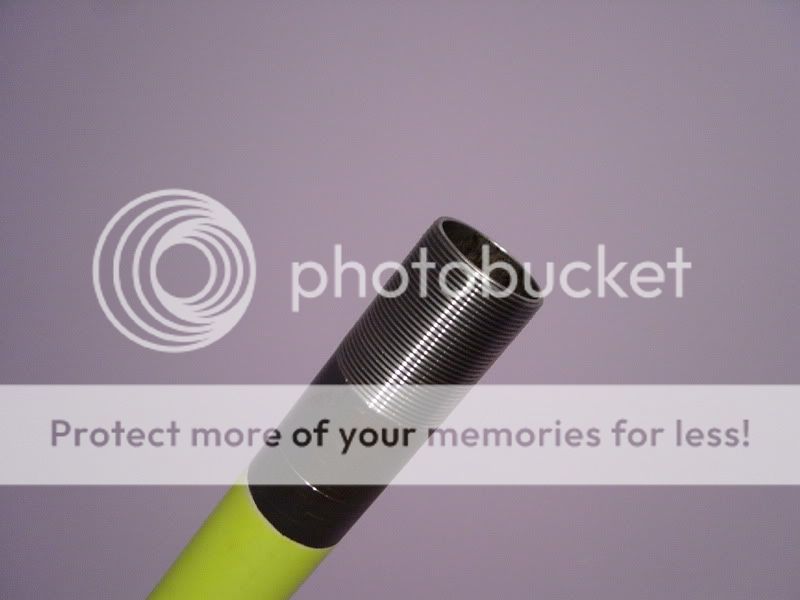
It works perfectly :
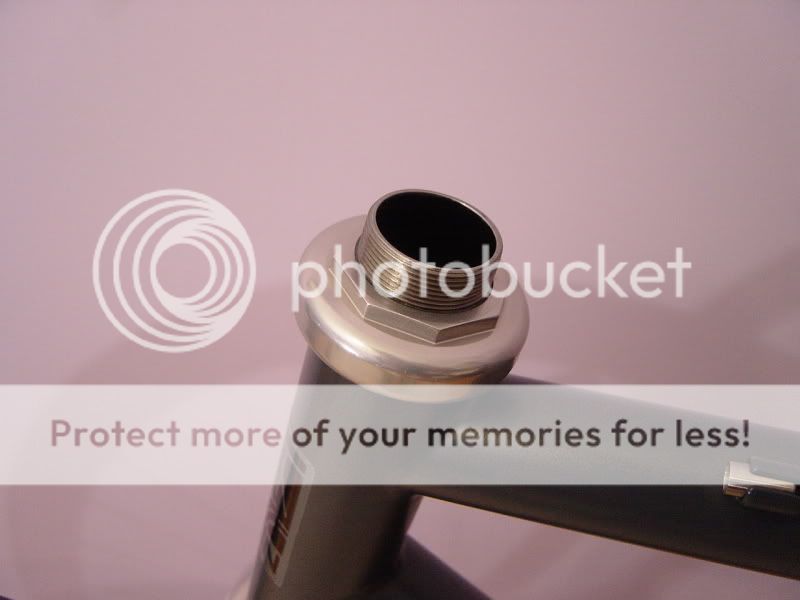
Hope that helps !
WD
