LumPi Panda
Retro Guru
- Feedback
- View
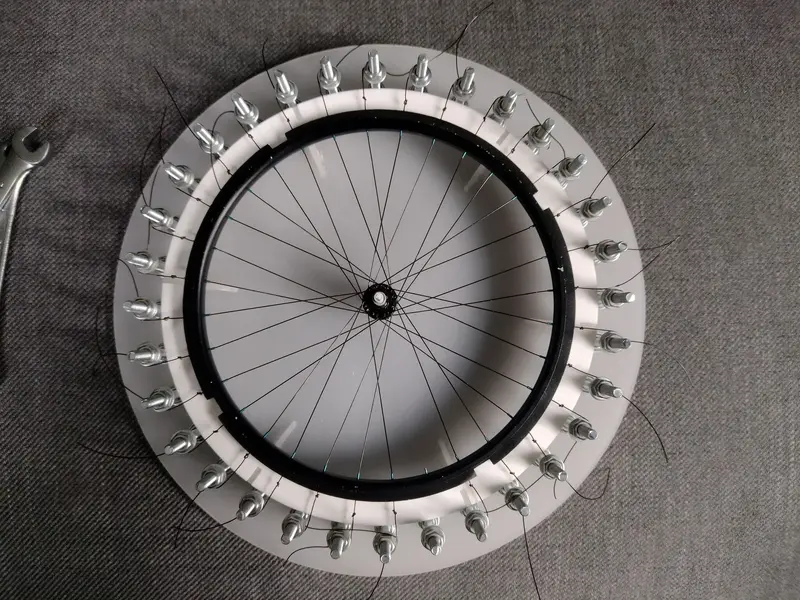
Wheelbuilding, quarter scale.
The spindle in the middle holds the hub at the correct height relative to the white ring holding the rim. Different spindles are used for the front and rear hub. Lengths of monofilament fishing line are laced as spokes having melted a small "spoke head" on the end using FIRE.

The knot in the filament outside the rim is tied as close to the rim as possible, these will be used to secure each spoke with superglue once the wheel is trued. Without the knot, the monofilament just slips through superglue, which is a pain in the horse. During the tensioning and truing, if a knot goes beyond the outside of the white ring it must be retied further in so it will fit inside the tyre carcass later.
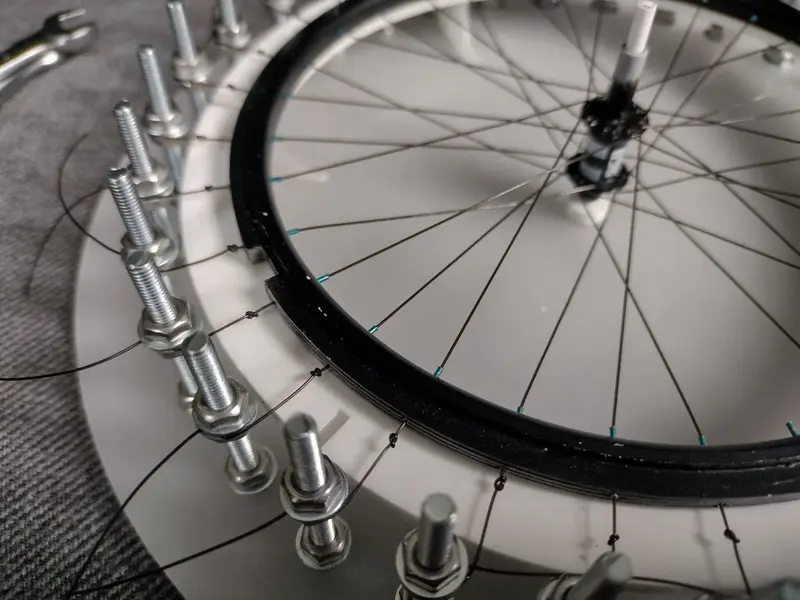
By tightening and untightening each set of nuts, the rim ends up just lifted up from the ring. Only just enough to go "click" instead of "thud" when it is tapped.
I need to get out more.
Last edited: