Jonny69
Senior Retro Guru
3D printed arm has arrived! Side by side you can see a small mistake I made on my CAD model for the tension spring slot. I’m annoyed at myself about that. It won’t affect the function but it’s a timely reminder to always measure twice and cut once.
This is my first ever 3D print in metal. I opted for a bead blasted finish to take off the as-printed roughness and this was the right thing to do. Tolerances are within 0.1mm. Internal bores are within tolerance but have a bead-blasted finish, so I’d recommend taking that into account as they’ll need re-finishing if it’s a bearing surface. I made mine slightly undersized to take up some of the wear and I’ve lightly honed it by hand to suit the pivot. I’ll also need to smooth off the side faces, but I’ll do that once I’ve refreshed my memory how it goes back together.
Once I’ve lapped all the parts together, it should work as good as, if not better than original! I might use a bit of fine valve grinding paste to just bed everything together nicely.
Edit: also I needn’t have worried about the stiffness. It’s easily as stiff as the original and it feels like the bead blasting has eliminated any stress risers which would be present in an as-printed surface finish.
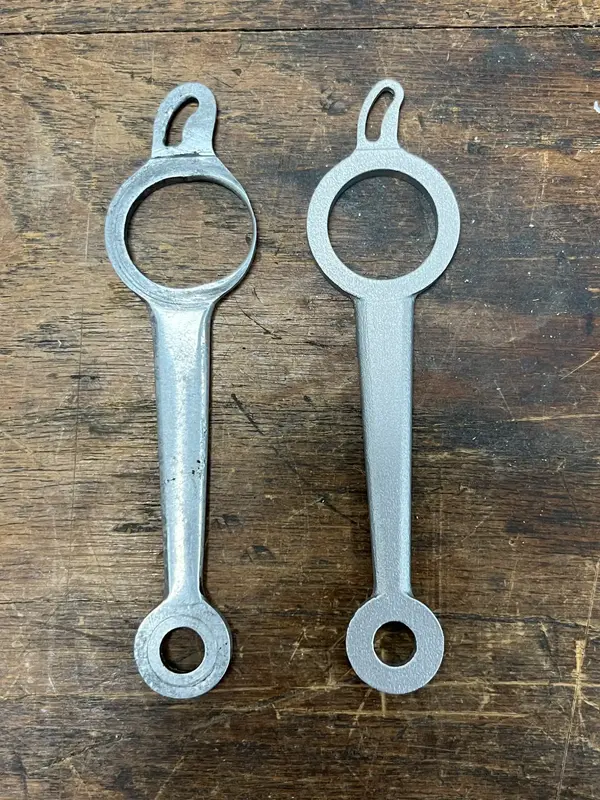
This is my first ever 3D print in metal. I opted for a bead blasted finish to take off the as-printed roughness and this was the right thing to do. Tolerances are within 0.1mm. Internal bores are within tolerance but have a bead-blasted finish, so I’d recommend taking that into account as they’ll need re-finishing if it’s a bearing surface. I made mine slightly undersized to take up some of the wear and I’ve lightly honed it by hand to suit the pivot. I’ll also need to smooth off the side faces, but I’ll do that once I’ve refreshed my memory how it goes back together.
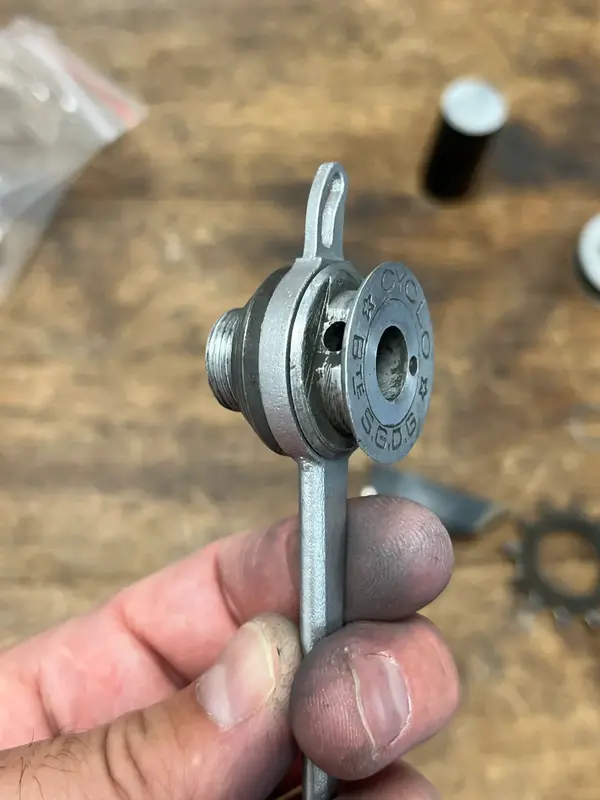
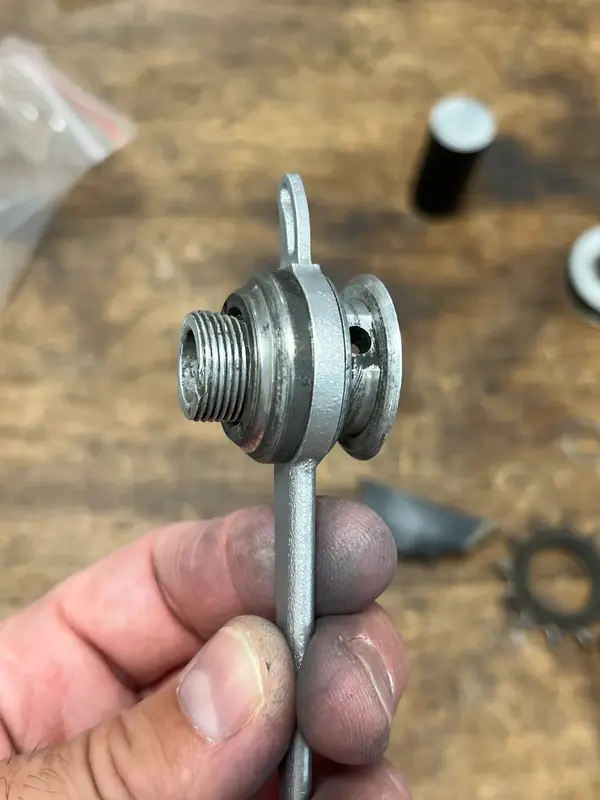
Once I’ve lapped all the parts together, it should work as good as, if not better than original! I might use a bit of fine valve grinding paste to just bed everything together nicely.
Edit: also I needn’t have worried about the stiffness. It’s easily as stiff as the original and it feels like the bead blasting has eliminated any stress risers which would be present in an as-printed surface finish.