rmwesley
Retro Guru
A couple of people asked if I could post up some pics and a parts list for my wheel jig. You might be underwhelmed since it is uber-simple to put together. Hopefully pictures speak a thousand words in terms of how it all goes together. Excluding the DTI gauges I think the whole thing cost less than £200.
The frame is made from aluminium profile purchased from motedis.co.uk. The base is 480mm wide by 440mm deep & the vertical posts are 660mm tall. I've built a few jigs and frames for fish tanks etc. and motedis are by far and away the cheapest / easiest company to deal with if you are only buying small amounts.
Parts
Base (front centre): Profile 40x40L I-Type slot 8 (019600 - 400mm)
Base (left and right): Profile 40x40L I-Type slot 8 (019600 - 360mm)
Base (rear centre): Profile 40x80L I-type slot 8 (019603 - 480mm)
Posts: Profile 40x80L I-type slot 8 (019603 - 660mm)
Base brackets: Bracket 40 I-Type slot 8 with fastening set and cover cap (S8IBR40)
Post brackets: Bracket 40x80 I-Type slot 8 with fastening kit and cover cap (S8IBR4080+FS+CC)
Cover caps: Cover Caps 40x80 I-Type slot 8 (091009)
Cover caps: Cover Caps 40x40 I-Type Slot 8 (091007)
Downside is a minimum shipping cost of approx. £15 - £20 for any order, so you can't really afford to miss anything off. I've got bags of nuts, fasteners and brackets & dipped into those for this build, so the list above is probably not exhaustive. If you have a crack yourself, figure out exactly what you need.
The steel base plate is 480mm wide x 400mm deep x 10mm thick plate covered in Hammerite and bolted onto the frame securely. For this you will need the "Roll-in T-Nut I-Type slot 8" fasteners which go into the profile slots. They come in M4, M5, M6 and M8.
More to follow...
The frame is made from aluminium profile purchased from motedis.co.uk. The base is 480mm wide by 440mm deep & the vertical posts are 660mm tall. I've built a few jigs and frames for fish tanks etc. and motedis are by far and away the cheapest / easiest company to deal with if you are only buying small amounts.
Parts
Base (front centre): Profile 40x40L I-Type slot 8 (019600 - 400mm)
Base (left and right): Profile 40x40L I-Type slot 8 (019600 - 360mm)
Base (rear centre): Profile 40x80L I-type slot 8 (019603 - 480mm)
Posts: Profile 40x80L I-type slot 8 (019603 - 660mm)
Base brackets: Bracket 40 I-Type slot 8 with fastening set and cover cap (S8IBR40)
Post brackets: Bracket 40x80 I-Type slot 8 with fastening kit and cover cap (S8IBR4080+FS+CC)
Cover caps: Cover Caps 40x80 I-Type slot 8 (091009)
Cover caps: Cover Caps 40x40 I-Type Slot 8 (091007)
Downside is a minimum shipping cost of approx. £15 - £20 for any order, so you can't really afford to miss anything off. I've got bags of nuts, fasteners and brackets & dipped into those for this build, so the list above is probably not exhaustive. If you have a crack yourself, figure out exactly what you need.
The steel base plate is 480mm wide x 400mm deep x 10mm thick plate covered in Hammerite and bolted onto the frame securely. For this you will need the "Roll-in T-Nut I-Type slot 8" fasteners which go into the profile slots. They come in M4, M5, M6 and M8.
More to follow...
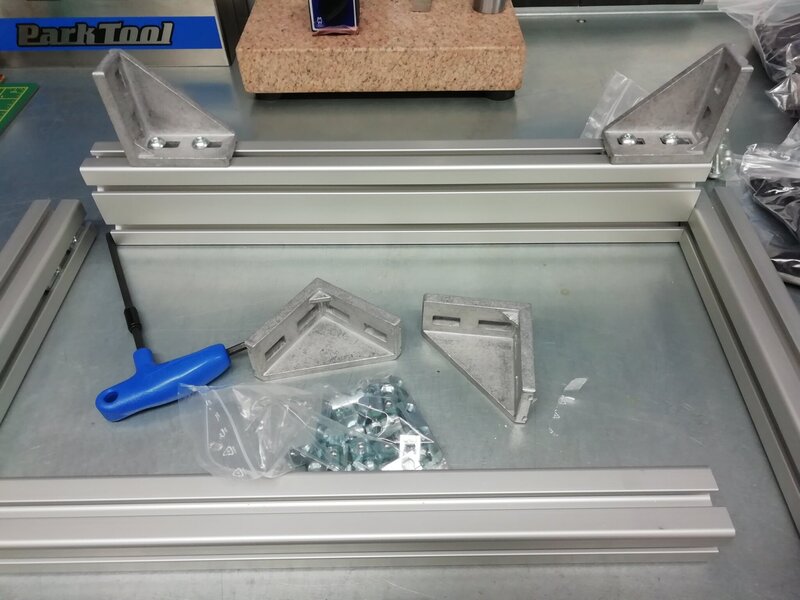
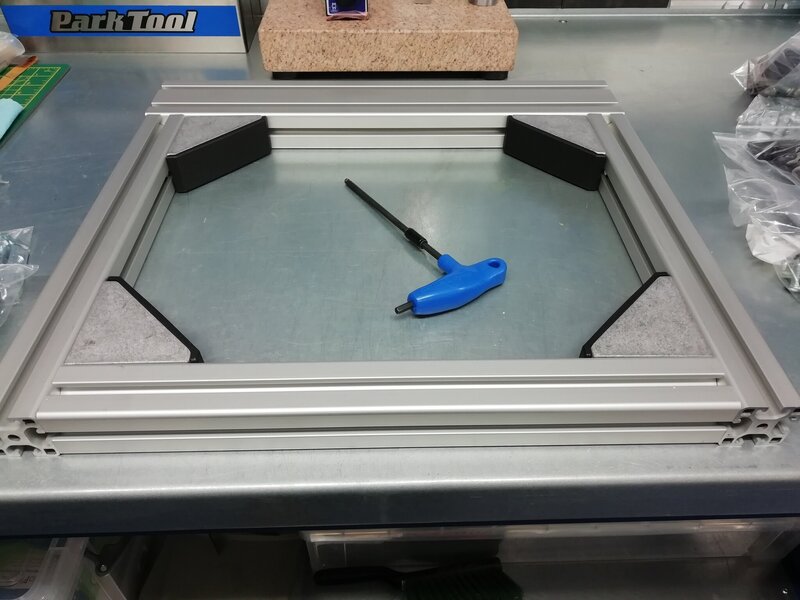
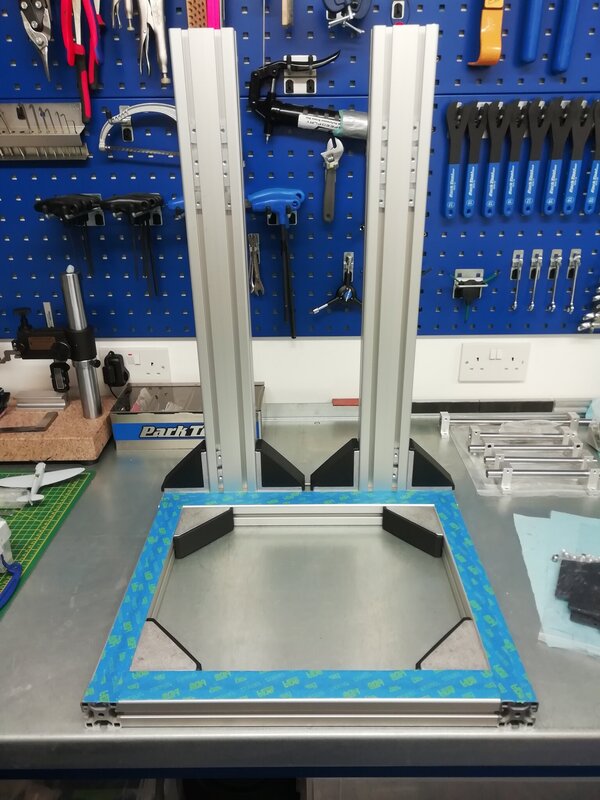
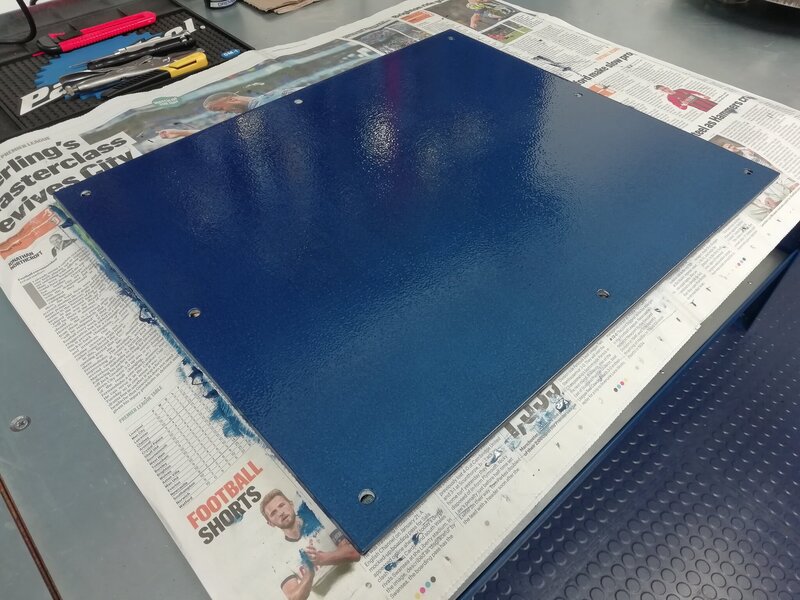
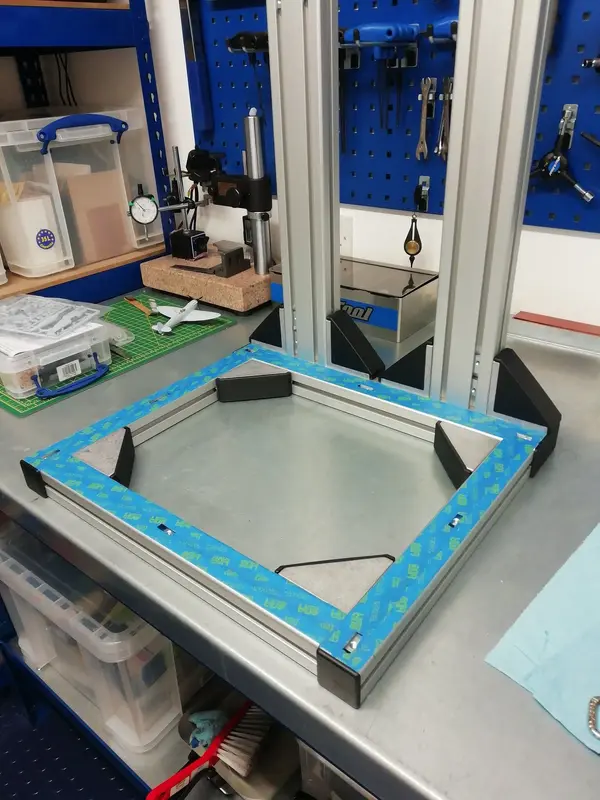
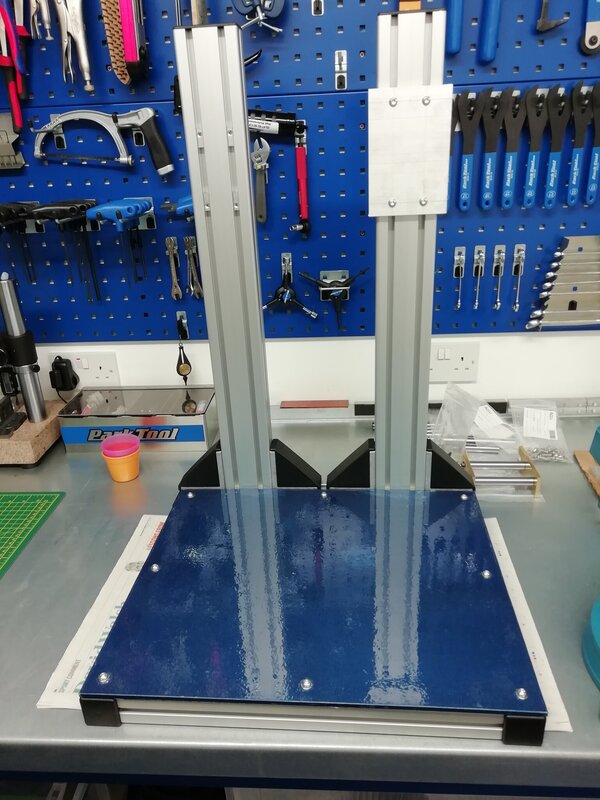
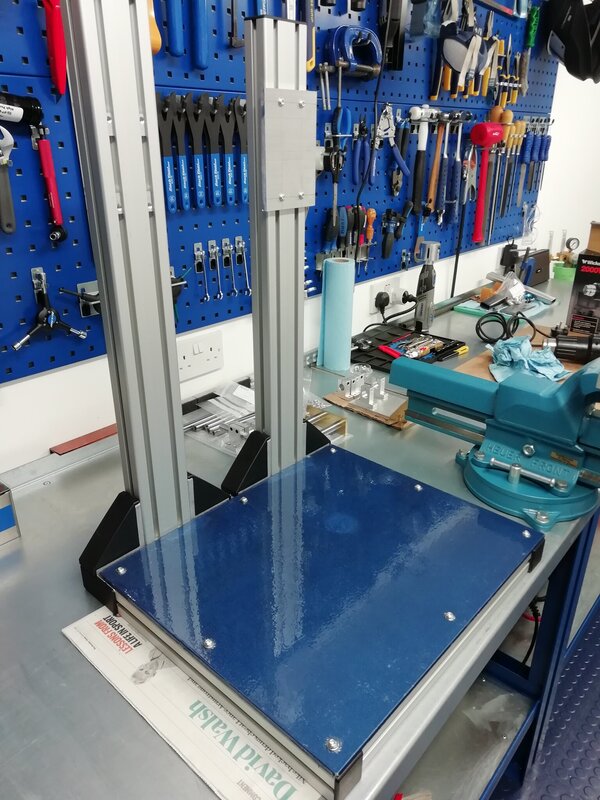