OK, here we go, with a few changes due to not receiving material from Ebay (man sometimes...)
Instead of 2 cross drive side, it´ll be 3 cross (as most use anyway) and non drive side will be radial, hub is 46mm hole to hole and there is enough flange material to do it safely. Let my just clear up that radial lacing on front hubs should not be done on hubs with more than 28 holes, due to the smaller hole to hole diameter (this hub I´m using is 40mm H/H) if it had been a 32 or 36 hole hub, the diameter would still have been 40mm with less material in the flange.
I have already built the front, since it´s straight forward I did not take pictures of the build, but here are some pics of the finished wheel.
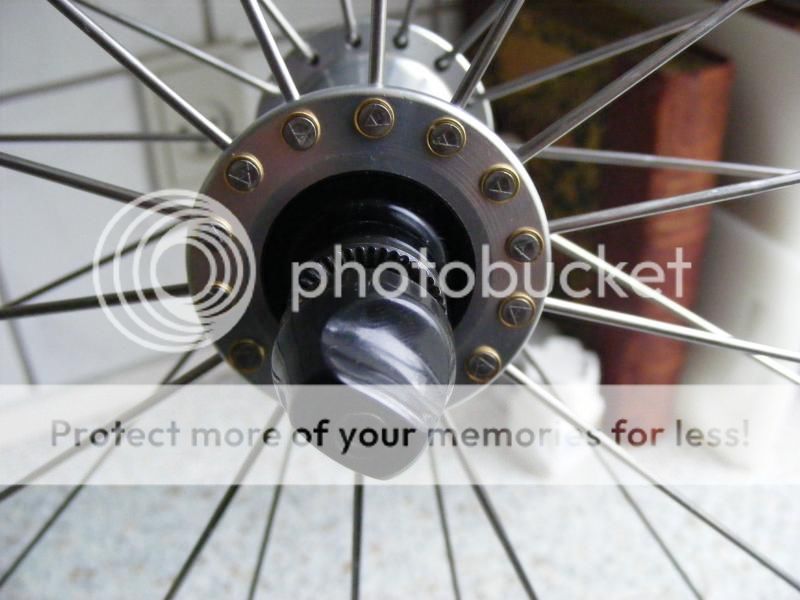
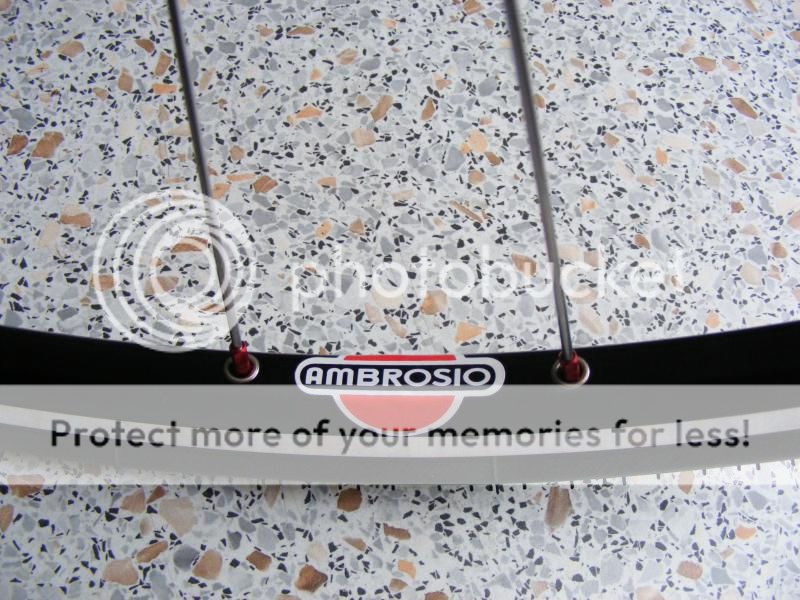
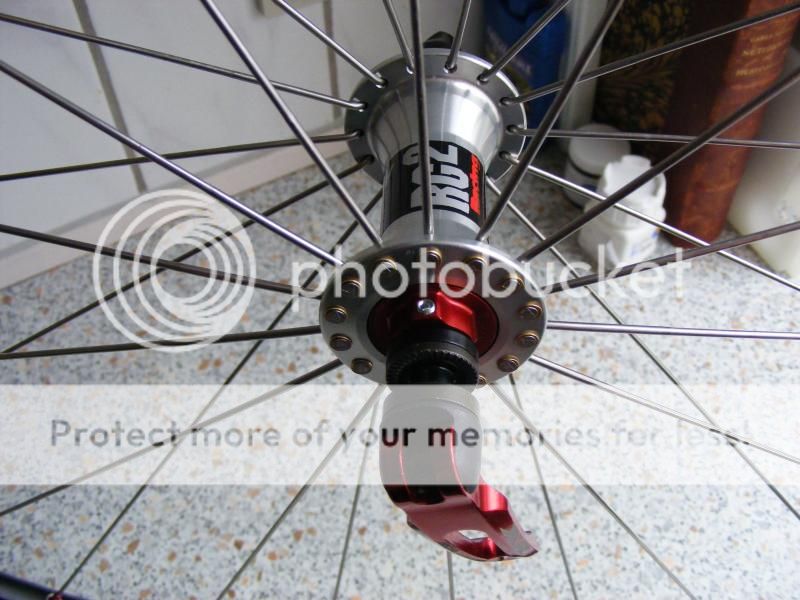
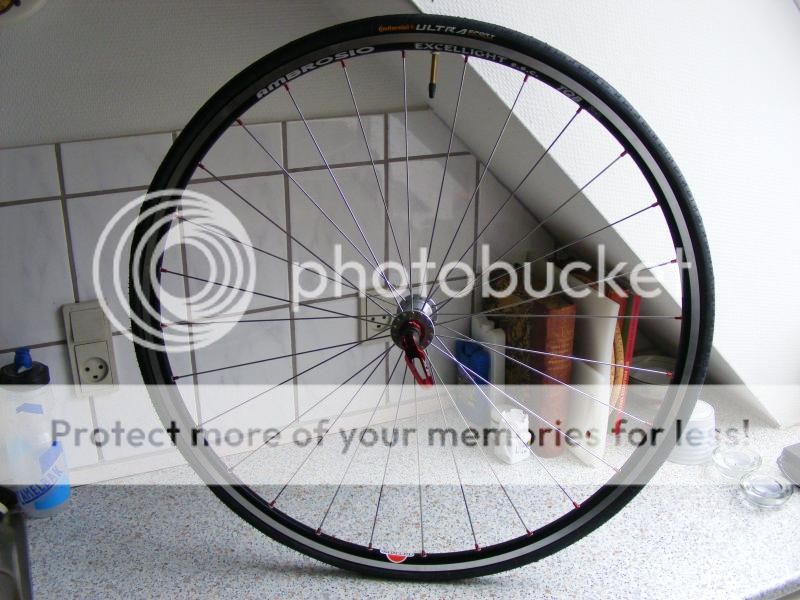
Instead of 2 cross drive side, it´ll be 3 cross (as most use anyway) and non drive side will be radial, hub is 46mm hole to hole and there is enough flange material to do it safely. Let my just clear up that radial lacing on front hubs should not be done on hubs with more than 28 holes, due to the smaller hole to hole diameter (this hub I´m using is 40mm H/H) if it had been a 32 or 36 hole hub, the diameter would still have been 40mm with less material in the flange.
I have already built the front, since it´s straight forward I did not take pictures of the build, but here are some pics of the finished wheel.
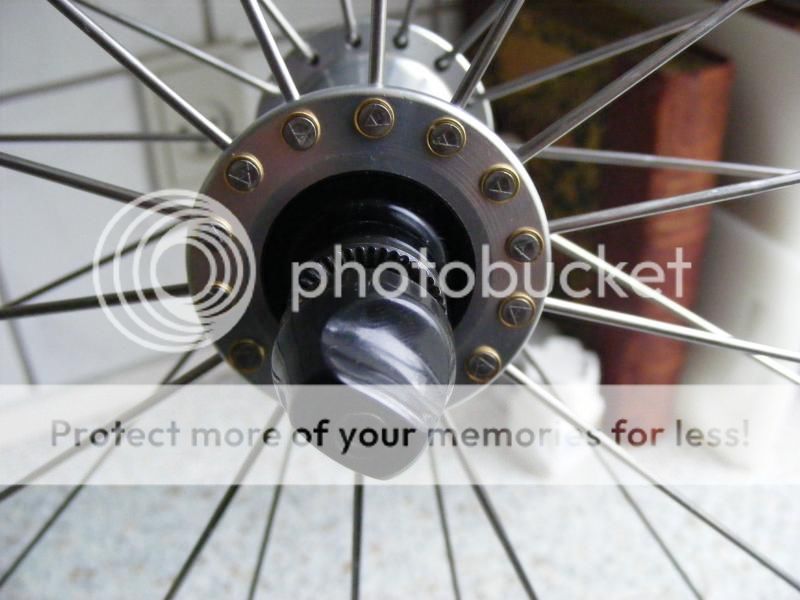
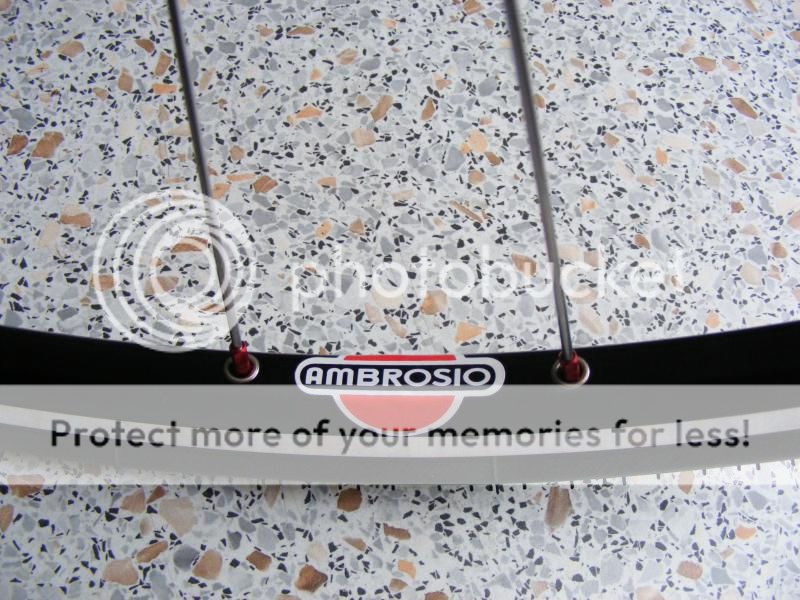
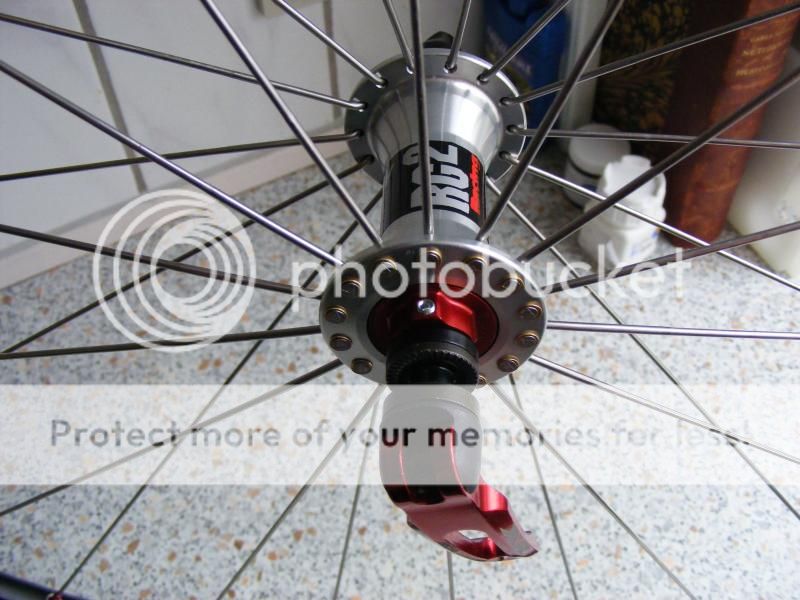
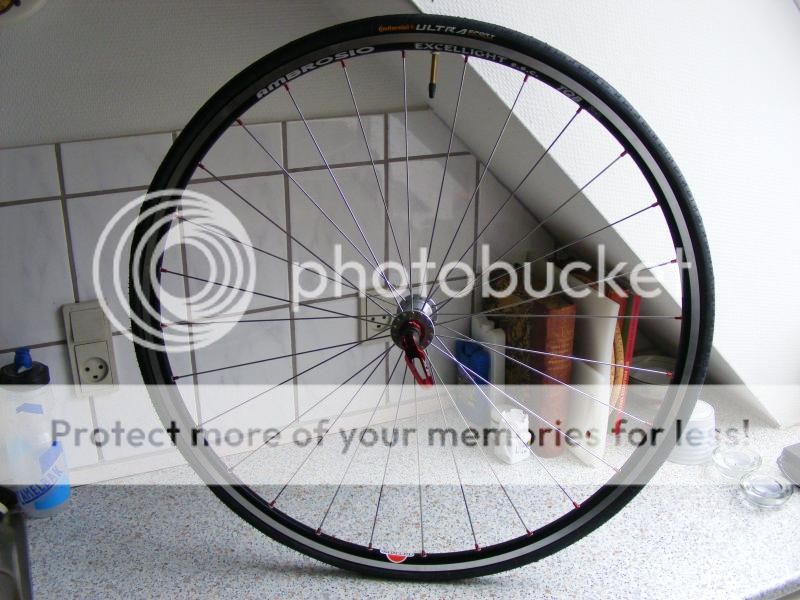