In true thereIfixedit.com style I have fixed the cable routing on my Trek 990 singletrack.
I'm using the frame as a basis for a rough stuff tourer and the standard front mech cable routing is just plain silly. LGF has an ingenious work around using a brake noodle:
I wanted a more permanent solution so out with the blow torch, silver braze and flux it was. I scavenged a cable stop and bottle cage boss from a scrap frame and this is the result, on Trek 990 with sensible cable routing and a front mech pulley that lets me run top or bottom pull mechs. While I was at it I filled some chain suck damage and fitted a chain pip in the inside of the chain stay (hence the scorching to the paint on the outside).
Not perfect but it will do. The fillet round the bottle cage boss is acceptable. It's quite simple to do, cheapest blow torch I could get from screwfix that I usually use for heating stuck BBs and a length of silver braze and some flux powder. Ideal for small jobs like this but will never get hot enough for structural repairs.
The key is getting it clean, file paint off down to bare metal, get all the bits of paint off with coarse sand paper. Prep the braze ons in the same way, you need gleaming steel with no signs of rust or paint. Mix a drop of water with some flux powder to form a paste and paint on to the area you want the brake to stick to. Heat the brazing rod with your blow torch to warm it up and dip the top inch in to the flux powder, powder will stick to it (called hot rodding don't you know). Put brazeon on the frame, heat, when the flux paste starts to run clear it's about hot enough. Touch the brazing rod against the join, keeping the heat on, and you should see it melt and flow along forming a beautiful fillet. It's really satisfying when it works. Wait for it to cool then clean off the flux residue (it goes black when it's exhausted). Importantly tap any cable stops etc with a hammer to make sure the join is strong. The last thing you want to do is to send the thing off for painting and them to fall off when the bike is assembled.
Now to find a brake cable hanger for the rear cantis.
Any who, that is what I did this lunch time. (I also took a file to the TREK that was cast in to the seat stay cluster.)
I'm using the frame as a basis for a rough stuff tourer and the standard front mech cable routing is just plain silly. LGF has an ingenious work around using a brake noodle:
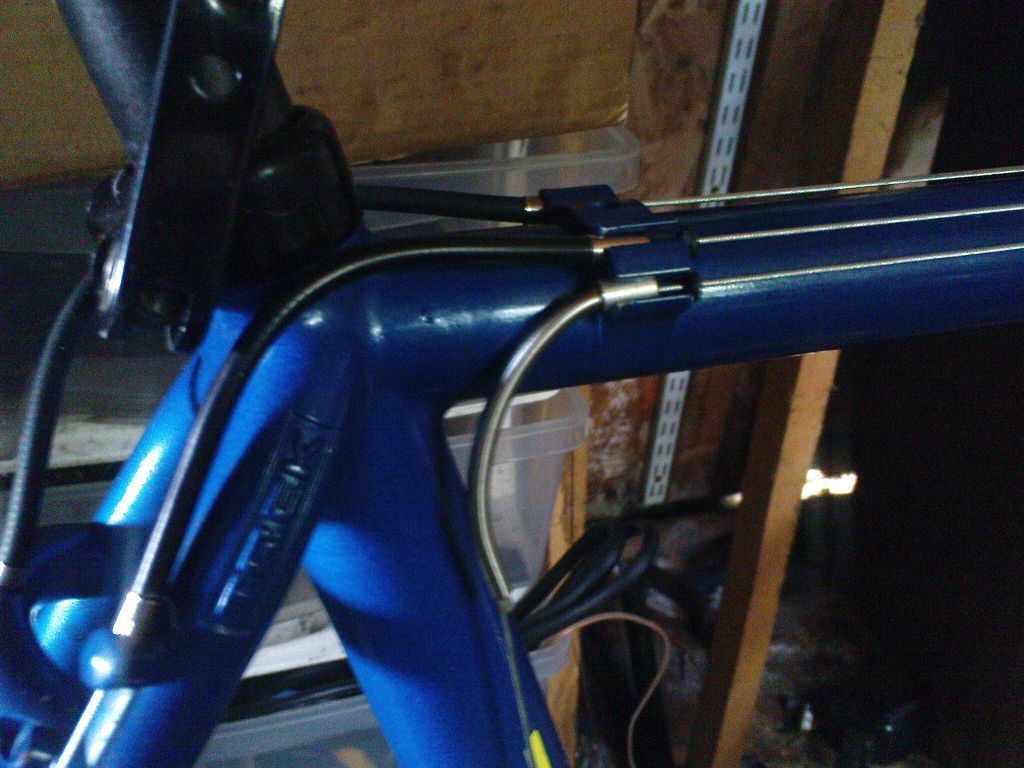
I wanted a more permanent solution so out with the blow torch, silver braze and flux it was. I scavenged a cable stop and bottle cage boss from a scrap frame and this is the result, on Trek 990 with sensible cable routing and a front mech pulley that lets me run top or bottom pull mechs. While I was at it I filled some chain suck damage and fitted a chain pip in the inside of the chain stay (hence the scorching to the paint on the outside).
Not perfect but it will do. The fillet round the bottle cage boss is acceptable. It's quite simple to do, cheapest blow torch I could get from screwfix that I usually use for heating stuck BBs and a length of silver braze and some flux powder. Ideal for small jobs like this but will never get hot enough for structural repairs.
The key is getting it clean, file paint off down to bare metal, get all the bits of paint off with coarse sand paper. Prep the braze ons in the same way, you need gleaming steel with no signs of rust or paint. Mix a drop of water with some flux powder to form a paste and paint on to the area you want the brake to stick to. Heat the brazing rod with your blow torch to warm it up and dip the top inch in to the flux powder, powder will stick to it (called hot rodding don't you know). Put brazeon on the frame, heat, when the flux paste starts to run clear it's about hot enough. Touch the brazing rod against the join, keeping the heat on, and you should see it melt and flow along forming a beautiful fillet. It's really satisfying when it works. Wait for it to cool then clean off the flux residue (it goes black when it's exhausted). Importantly tap any cable stops etc with a hammer to make sure the join is strong. The last thing you want to do is to send the thing off for painting and them to fall off when the bike is assembled.
Now to find a brake cable hanger for the rear cantis.
Any who, that is what I did this lunch time. (I also took a file to the TREK that was cast in to the seat stay cluster.)